
SANGMIN SUNG
General Portfolio

MY BIO
I am a mechanical engineering major studying product design at University of California, Berkeley for the Meng program. I have a great passion for engineering because I enjoy implementing the fundamental knowledge of engineering and utilizing CAD software, 3D printing and prototyping to build things that resemble real world applications.
During my education, I have consistently worked on several projects with intelligent people from different backgrounds.
From small, solo projects to creative collaborations, I’m always looking for the chance to explore and learn something new that I can apply to my works.
PROJECTS
Projects done at California Polytechnic State University SLO

FLUID POWER VEHICLE CHALLENGE
April 2021- April 2022
Fluid Power Vehicle Challenge focused on iterating on and designing a fluid powered vehicle that would perform well in the annual Fluid Power Vehicle Challenge, hosted by two fluid power companies, Danfoss Power Solutions and Norgren. The competition was based on three physical challenges: sprint challenge, endurance challenge, and efficiency challenge. To build a competition’s winning design, my team focused on the following implementations: a composite frame design in the hopes of reducing overall vehicle weight, hydraulic hardlines to reduce the overall loss of hydraulic power in the system, a custom user interface that would actuate valves and acquire data, and a pneumatic adjustable seat with double acting pneumatic actuator.
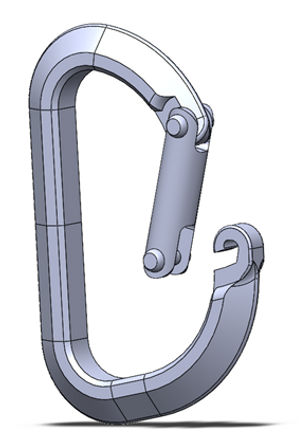
CARABINER
October 2020- November 2020
As a prototype for an aluminum 3D printed carabiner, the PLA design was to be tested at a scaled fraction of the requirements of an actual climbing carabiner. The carabiner was designed to sustain 300 lbs open gate load and 900 lbs closed gate load.

WOOD CHIPPER
February 2021- March 2021
With the rising desire to chip trees in California to reduce the area of possible burns and turn the discarded wood into smaller, reusable pieces, a design team was tasked with producing a new woodchipper drivetrain and cutting design. The project hoped to make a smaller, self-contained chipper that could handle smaller pine and oak branches up to 4” in diameter. It was also assumed that the frame and casing for both towing the chipper and directing the chips after cutting were being handled by another team. As such, the major components that would need major design consideration from the design team were the chipper shaft, flywheel, bearings, motor selection, and power transmission components.
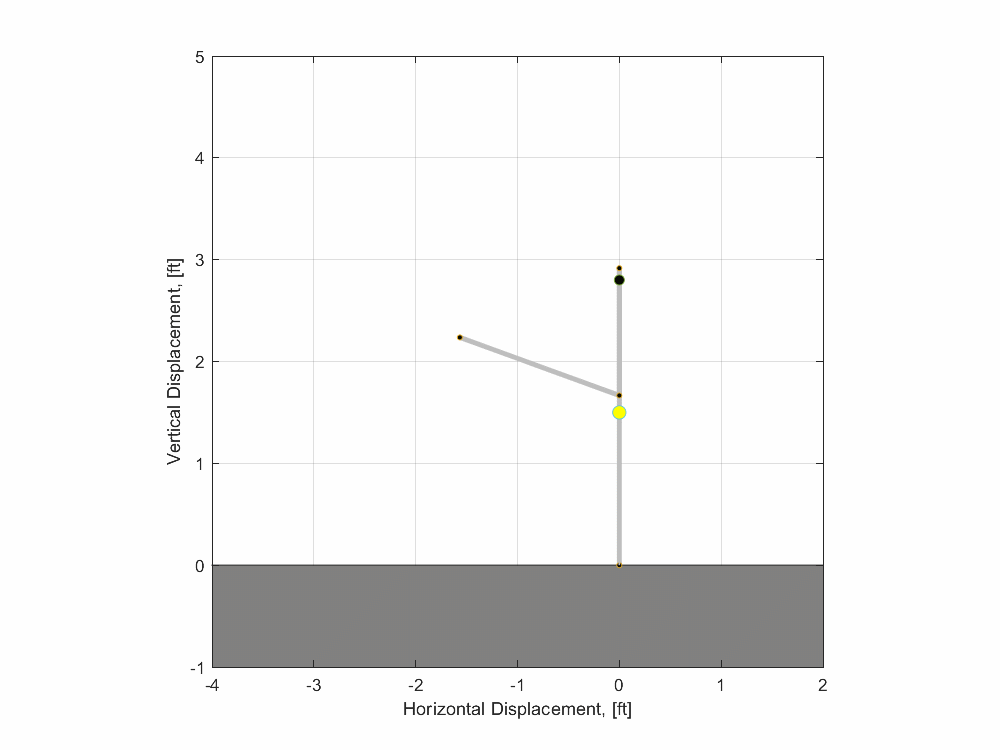
DYNAMICS WITH MATLAB
Cal Poly Mechanical Engineering students take various mechanics classes that help develop the necessary skills for design and analysis of complex systems.
We have a three course series of System Dynamics, Dynamics, and Intermediate Dynamics. The link below contains the laboratory works and projects completed during the dynamic courses

MECHATRONICS
October 2021-December 2022
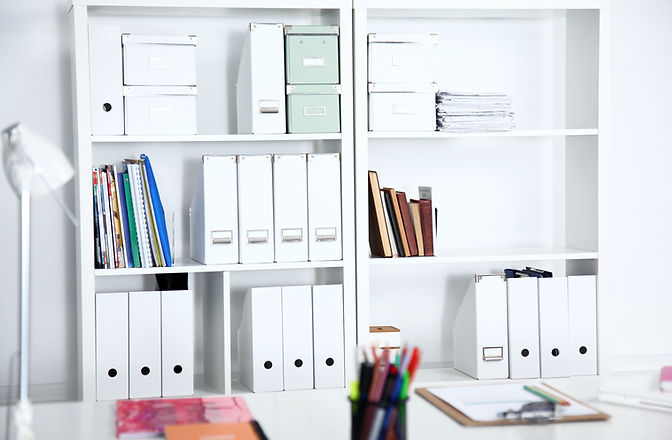
PROJECT
Perfect Execution
This is your Project description. Whether your work is based on text, images, videos or a different medium, providing a brief summary will help visitors understand the context and background. Then use the media section to showcase your project!
Radiant Heating System Design
The objective of this project is to design a radiant heating system to heat up the atrium of a community center in Atascadero, California. The system should heat up the atrium via water pumped through coiled PVC piping embedded in the concrete floor of the atrium. The design of the system is analyzed in three ways: 2-D Conduction analysis, 2-D Transient analysis, and Heat Transfer in Pipe Flow analysis. Each analysis is thoroughly done via EES (shown in the report file) and excel and can be found in the files below.
Projects done at University of California, Berkeley
PASSIVE BODY ARMOR EXOSKELETON
Capstone Project (Sept 2022-May 2023)
The objective of this project is to design a low-cost passive body armor exoskeleton that provides dynamics and maneuverability and reduces metabolic cost of musculoskeletal injuries caused by heavily induced loads on shoulder. This project is sponsored by suitX, and our team was given an exoskeleton product that we could manipulate it to be viable for supporting body armor passively. In doing so, our team focused on resolving two main design problems that the provided exoskeleton product had:
The wearer felt difficult to bend forward due to rigidly attached spinal connection to the shoulder component without any flexibility.
When bending forward, the wearer’s shirt kept getting pulled up by the back support.
The solution to the addressed problems is implemented using a latch design that involves 3D rapid prototyping using 3D printers and 3D modeling. The link below shows detailed descriptions of this project
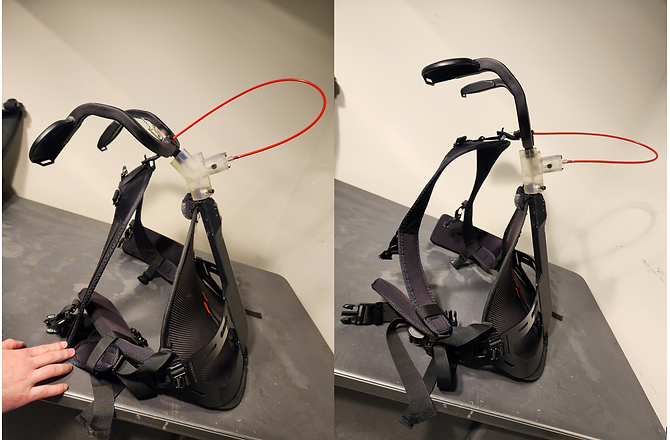
PASSIVE BACK EXOSKELETON
January 2023-May 2023
Many construction workers have been experiencing back injuries from carrying heavy loads for a long time. In order to help them minimize their injuries, I worked on building a back passive exoskeleton that can be cheap and be very effective on reducing the loads induced at the back.
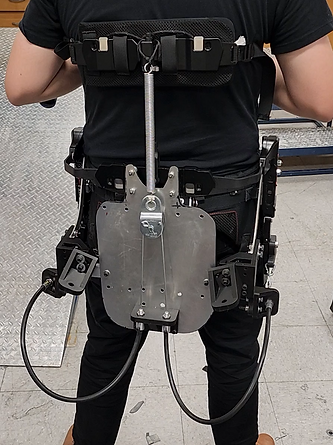

PASSIVE PROSTHETIC FINGERS
Feb 2023- May 2023
For a patient who has lost his middle and index fingers, I designed a passive prosthetic fingers that would help him achieve stable gripping. This was a class project for human dexterity class at UC Berkeley. More descriptions of this device is in the link below.
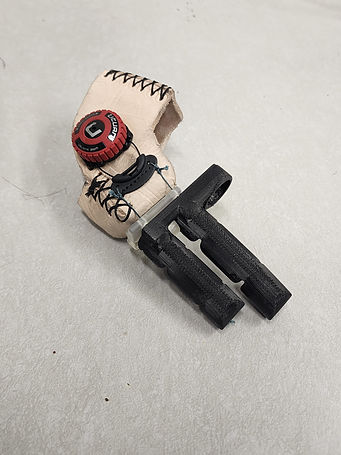.jpg)
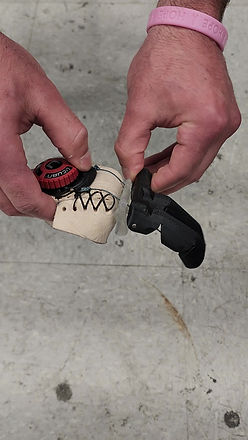